Schneider Messtechnik: On Board for 35 Years!
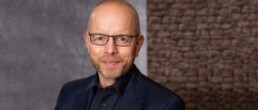
Uwe J. Keller, CMO at Dr. Heinrich Schneider Messtechnik GmbH in Bad Kreuznach, Germany (Photo: Schneider Messtechnik)
Control is the most important trade fair of the year for Schneider Messtechnik. The company from Bad Kreuznach was one of Control’s very first exhibitors. Uwe J. Keller, chief marketing officer at Schneider Messtechnik, talks about the importance of Control as the leading trade fair for quality assurance and current trends in the field of measuring technology.
Control has evolved into a permanent entry in the trade fair calendar for the entire metrology sector. Schneider Messtechnik has been an exhibitor from the very beginning and we’ve been able to accompany Control without interruption right on up to this year’s 35th event at the Stuttgart Exhibition Centre. It is and has been our most important trade fair each year. We especially value the high concentration of expert visitors at Control, who come to the event with concrete projects and enter into dialogues with the exhibitors. We also applaud Control’s development into the leading trade fair for quality assurance.
Focus on Measuring Software
On the one hand, the fact that more and more attention is being focused on ensuring that measuring machines can be operated very easily and intuitively is one of the most important current technological trends in quality assurance. In this regard, special emphasis is placed on the measuring software, which should support the operator to the greatest possible extent. Since we at Schneider Messtechnik have SAPHIR as well as U-SOFT software at our disposal, both of which are developed in-house by ourselves, we’re responding to this demand from the market with our current version 7 and have implemented it to the satisfaction of our users. We clearly view the issue of automation as a further key trend. Here too, we’ve brought the individual machine types up to speed and can integrate all of our CNC measuring machines into partially or fully automated systems. Of course both of these trends also reflect the current labour market situation. On the one hand, more and more people need to be able to use and operate measuring machines and, on the other hand, the current lack of personnel has to be offset by automated processes. We’re meeting these challenges by offering our customers practical, time-tested solutions.
Measuring Machines are Becoming Significantly More Dynamic
In order to speed up measuring processes, measuring machines also have to become much more dynamic. Flashed images are essential in this respect in order to prevent the blurring of images due to motion. Our WMX range is mentioned here as an example in the field of wave measurement which, thanks to the matrix camera and a fully integrated rotary axis, is capable of optical 3D wave measurement while in motion. As a static pole for dynamic measurement, the WMX range is also set up on a granite base. V-CAD lightning is another highlight from Schneider Messtechnik, which can make impressive use of this speed advantage both in transmitted light mode and with multifunctional incident light. Thanks to its granite base, the V-CAD range can be set up vibration-free in any manufacturing environment. All processes are controlled synchronously by the new SAPHIR 7 software in order to quickly obtain valid measurement results.
Modern QA measures help to cope with production challenges such as efficiency, the conservation of resources and sustainability. In order to be able to create efficient processes, you have to be informed about the current status at every point throughout the process chain. Reliable quality assurance is indispensable in order to be able to represent this transparently. The fact that in the end, the conservation of resources and sustainability are also on board speaks for itself. Defective parts can be rejected immediately and are thus not passed on to downstream production steps. The consumption of energy and production resources is reduced. Ever-increasing reductions in the use of raw materials for components and the associated down-scaling necessitate more extensive production monitoring in order to be able to ensure functionality over the product’s entire service life.